Paper pulp solutions
Long fiber, short fiber. Strong and slim. Softwood pulp or hardwood pulp: We create pulp for most applications and solutions. Below you can find what pulp is best for you.
Dissolving pulp solutions
Clothes made from trees? Yes, it's possible. The dissolving pulp from Södra is mainly made from birch and is used in the textile industry for the production of viscose and lyocell.
OnceMore®
At present, no one in the world can recycle fibres from blended fabrics on a large scale. Södra now has a unique solution that will enable circular flows in the textile industry – we call this OnceMore®.
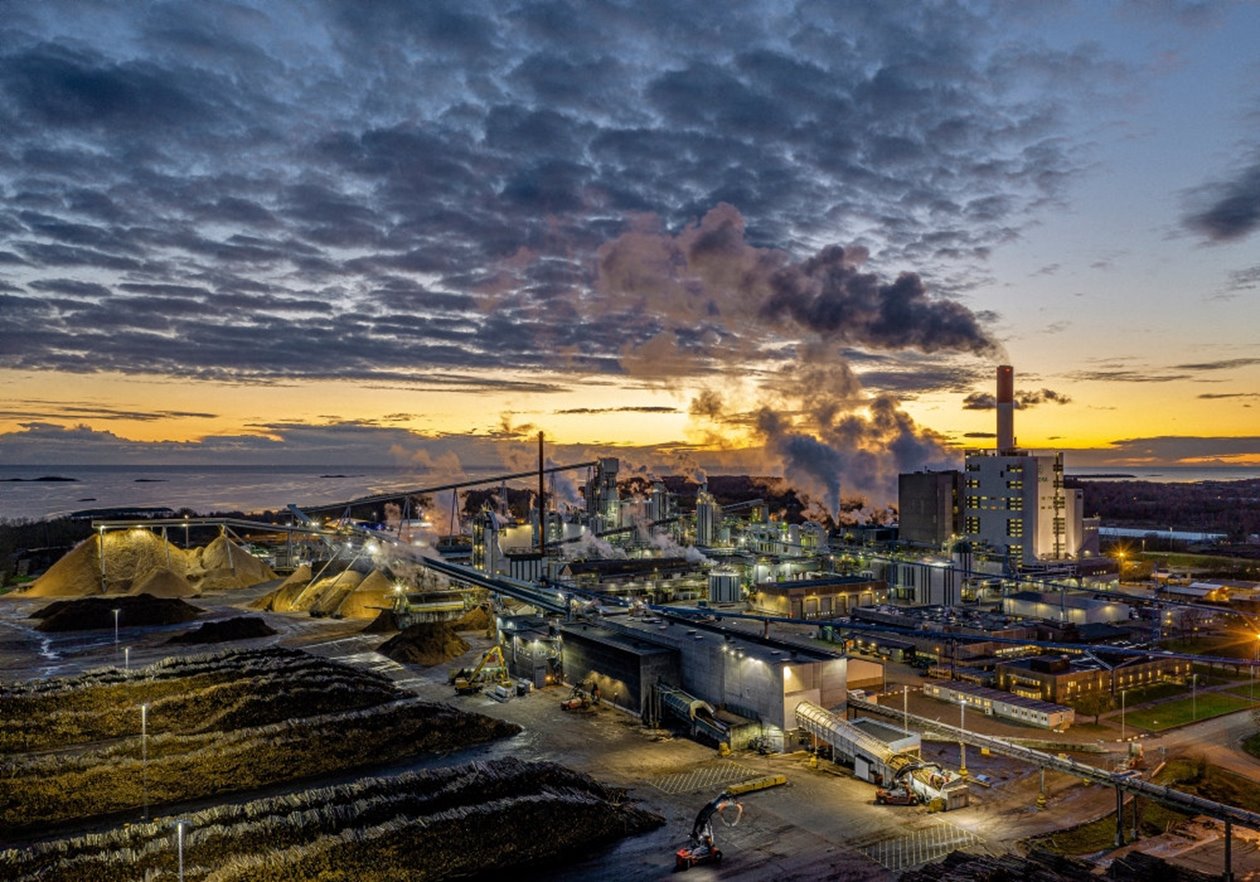
Our mills
Södra Cell is one of the world’s leading producers of paper pulp and dissolving pulp. Our three state-of-the-art pulp mills have a combined production capacity of 1.9 million tpy.
Our mill in Värö Our mill in Mönsterås Our mill in Mörrum
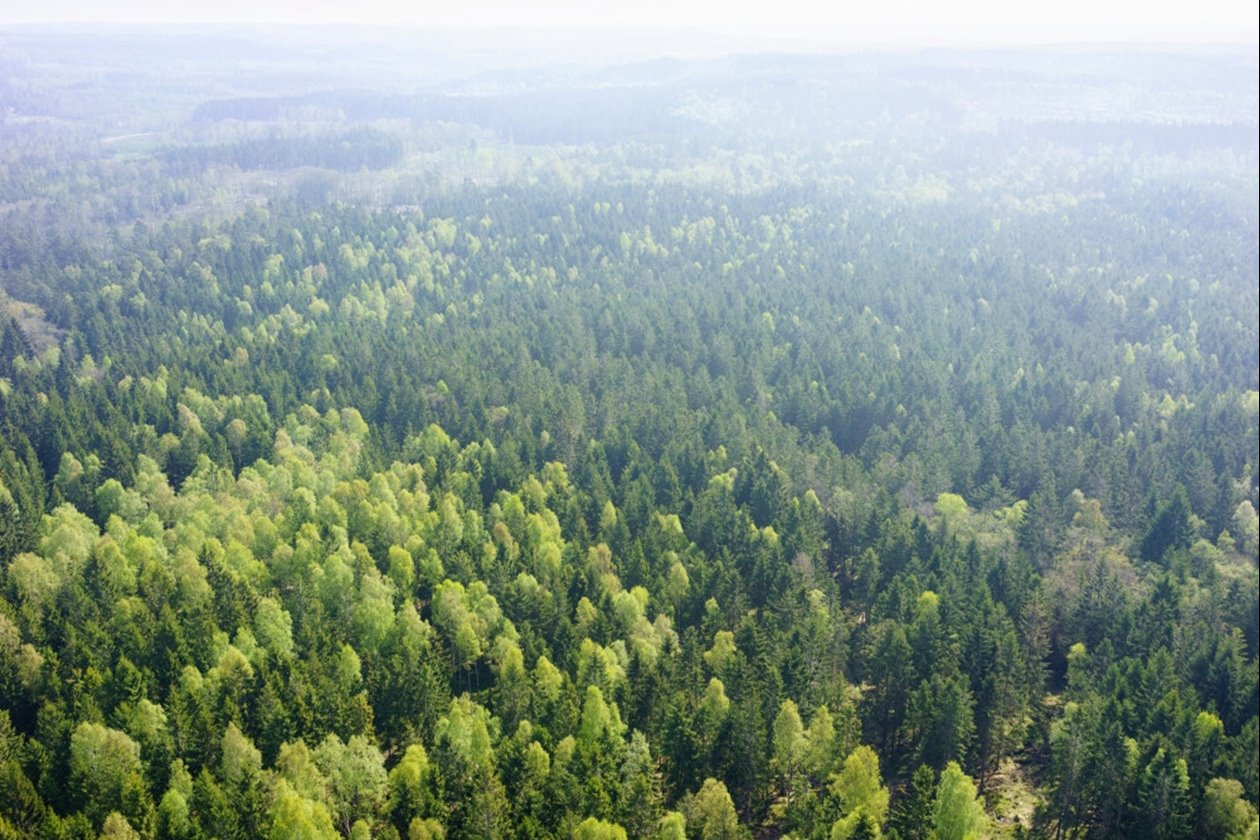
Always choose sustainable
Few things are more natural than wood products from the Swedish forest. We're one of Europe's largest suppliers of wood products for construction and almost all our wood comes from forests that have been nurtured for generations by our members. To maintain the highest standards of sustainability, we plant at least three new trees for each one we harvest, and our production is entirely fossil-fuel free.
Certifications Sustainability services Sustainability documents
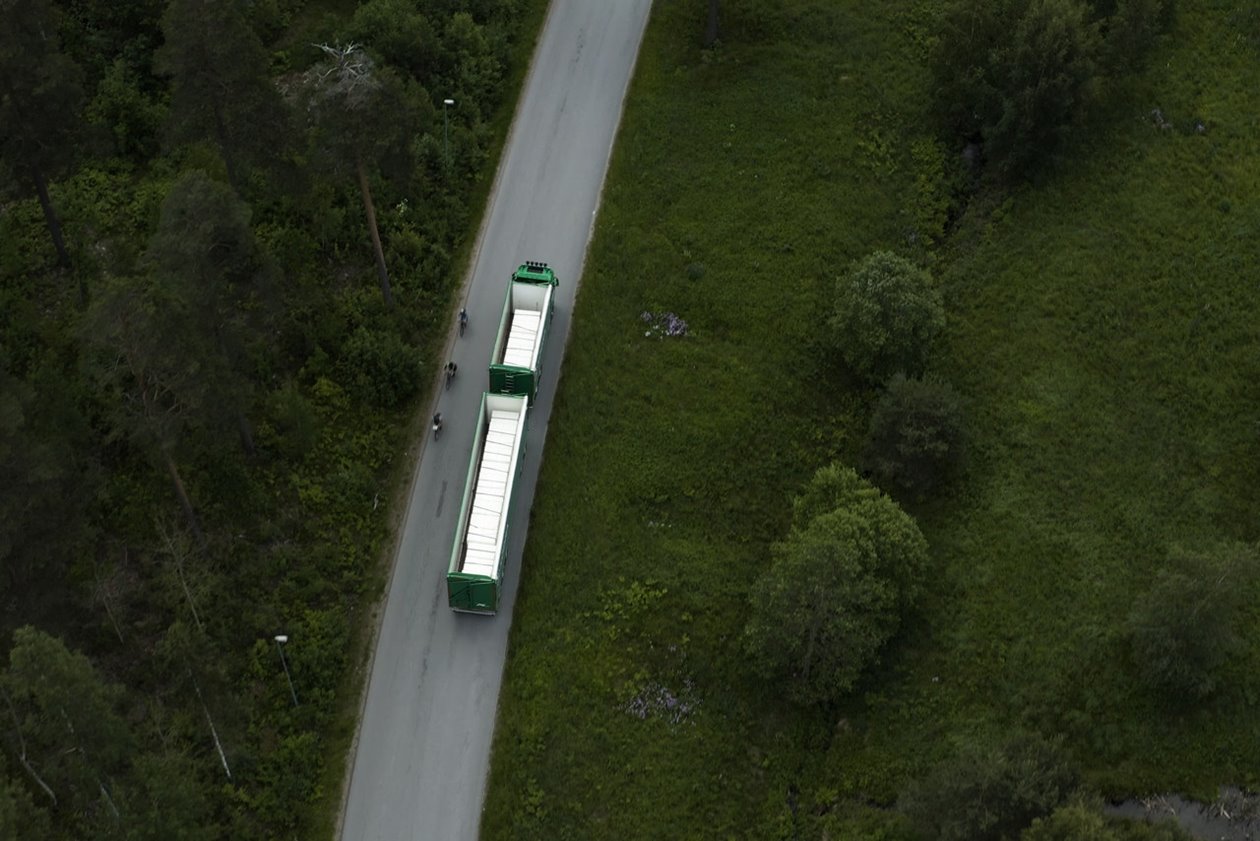
The future requires everyday heroes
The future requires everyday heroes and new ways of thinking. It can be as easy as actively choosing products from responsible-managed forests, but we also need to maximize our part as an industry and communicate our sustainability credentials to a wider audience beyond our immediate target market.

We love paper – pulp end uses
Milk packages, tissue paper, magazine paper or textiles. In every decision we make, big or small – we can make a difference. When choosing products that originate from sustainable forestry that’s exactly what you do. And making conscious choices – that’s our definition of heroism.
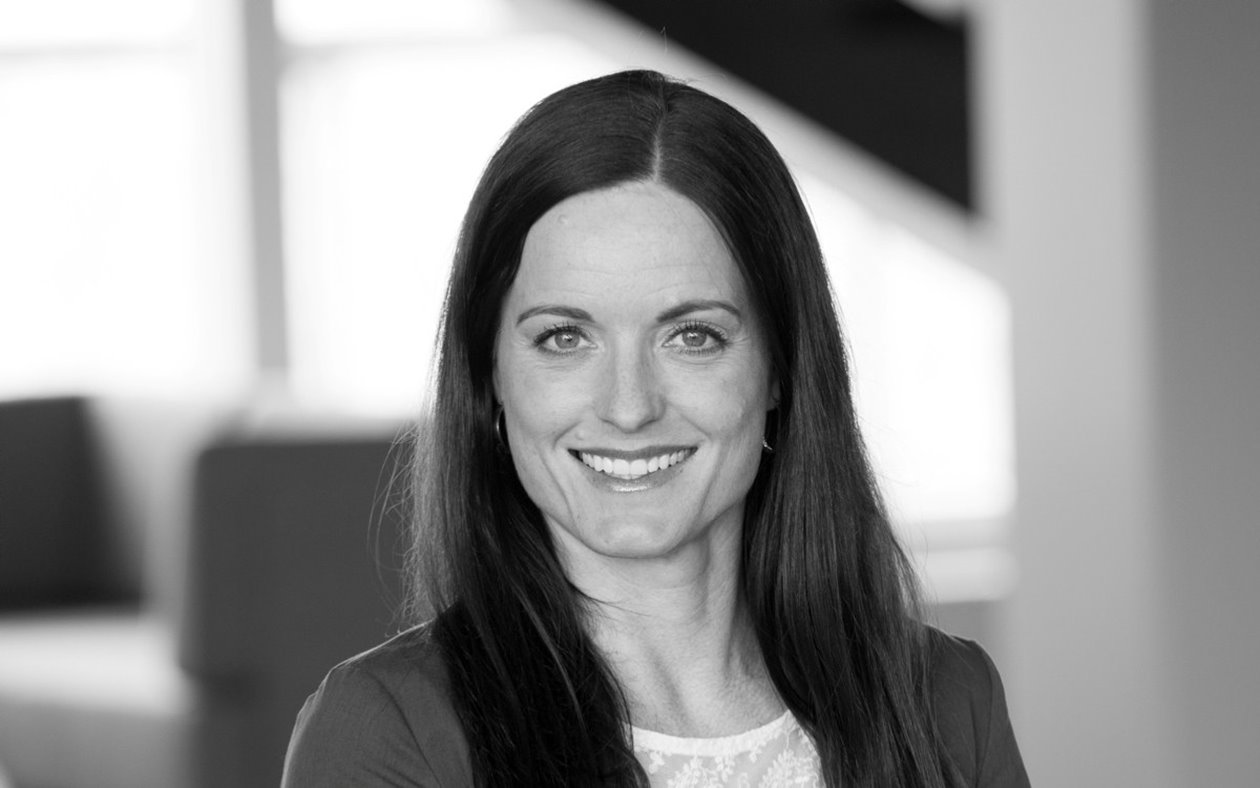
Contact us
It is important that you as our customer can easily get in touch with us at Södra. No matter what product or product category you are interested in, we have qualified teams who manage different functions to whom you can address inquiries of any kind.